Topics
Steine, Kies und Schotter – spannende Einblicke in wichtige Rohstoffe und effiziente Produktionsverfahren. Dies die wichtigsten Erkenntnisse aus einer Studienreise der Bahnjournalisten Schweiz in den Kanton Uri. Unter der Leitung von Lorenz Degen nutzen am 10. Mai 2023 ein Dutzend Mitglieder die Gelegenheit zum Besuch der Firmen Hartsteinwerk Gasperini AG in Attinghausen und Arnold & Co. AG in Flüelen.
Mehr über diese interessante Studienreise in diesem Bericht.
Firma Hartsteinwerk Gasperini AG
Um 10.15 Uhr begrüssten uns Michela Gasperini, Geschäftsführerin, und Peter Müller, Betriebsleiter, auf dem Betriebsgelände der Firma Hartsteinwerk Gasperini AG in Attinghausen. Für die Führung durch den eindrücklichen Steinbruch Eielen wurden zwei Gruppen gebildet.
Die Firma Gasperini wurde 1926 gegründet und wird heute in vierter Generation von Michela Gasperini geführt. Im Zuge einer Nachfolgeregelung wurde die Mehrheit am Unternehmen 2019 von der schweizweit tätigen Firma KIBAG AG übernommen. Gasperini beschäftigt zurzeit 21 Mitarbeitende und ist in der Region als Arbeitgeberin sehr geschätzt.
Im ersten Teil der Führung erläuterte uns Peter Müller die Organisation des Steinbruchs. Aus erstklassigem Quarzsandstein werden hochwertige Schotter, Splitte und Sande hergestellt. Der Schotter von Gasperini wird schweizweit eingesetzt und zählt wegen seiner Härte und Abreibfestigkeit zur absoluten Spitzenklasse der hiesigen Produkte.
Gasperini produziert in der Regel jährlich zwischen 40’000 und 70’000 Tonnen Bahnschotter – in Spitzenjahren sogar 100’000 Tonnen. Der Schotter wird mit Lastwagen zum benachbarten Bahnhof Altdorf transportiert und dort über die Verladeanlage auf Bahnwagen verladen. Im Gegensatz zu früher, wo mit einem Zug bis zu 800 Tonnen Schotter transportiert wurden, ist heute die Maximallast pro Zug wegen dem Mangel einer geeigneten Rangierlokomotive auf 400 Tonnen beschränkt. Infolge dieser Beschränkung erfolgen Lieferungen ins Tessin aber auch in der Deutschschweiz vermehrt mit Lastwagen.
Neben dem Schotter werden jährlich bis zu 160’000 Tonnen Edelsplitt, Sand und Strassenkoffer produziert. Die Produkte von Gasperini werden wegen ihrer hohen Qualität weit über die Standortregion hinaus eingesetzt.
Nach dieser interessanten Einführung erfolgt eine Besichtigung des eindrücklichen Abbaugebiets. Die Fahrt mit einem geländetauglichen Personenwagen führt über bis zu 35 Prozent steile Rampen zum obersten Abschnitt des Steinbruchs rund 280 Meter über dem Talgrund. Die Felsbrocken werden nach der Sprengung mit gewaltigen Dumpern zu den Steinbrechanlagen hinuntergefahren. Beladen erreichen die Dumper ein Gewicht von bis zu 52 Tonnen. Hoch oben erläutert uns Peter Müller die Felsformationen und den Ablauf der Abbauarbeiten. Die Sprengungen erfordern viel Knowhow und werden von der Firma Gasser Felstechnik AG ausgeführt.
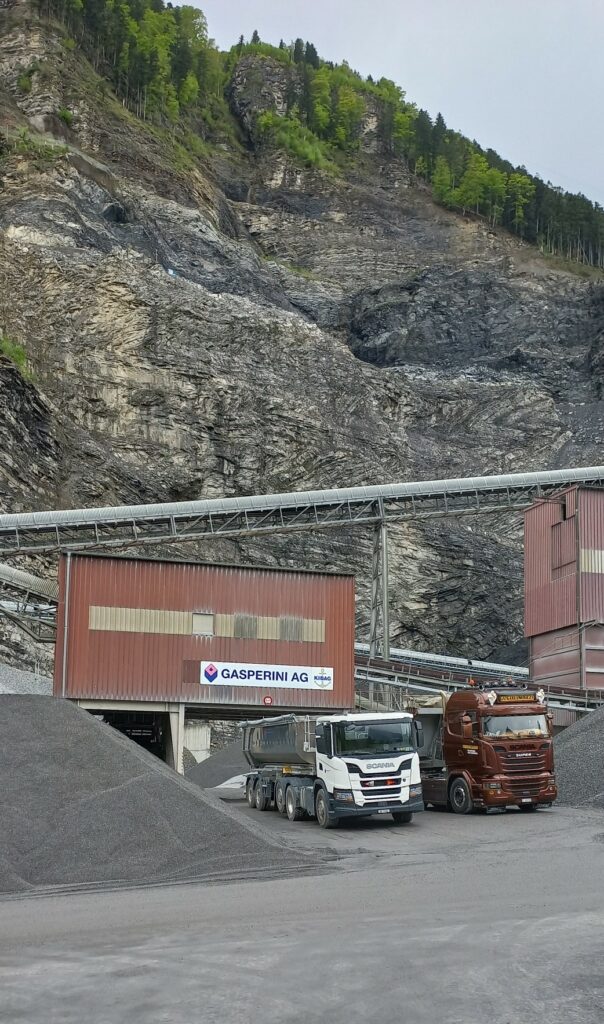
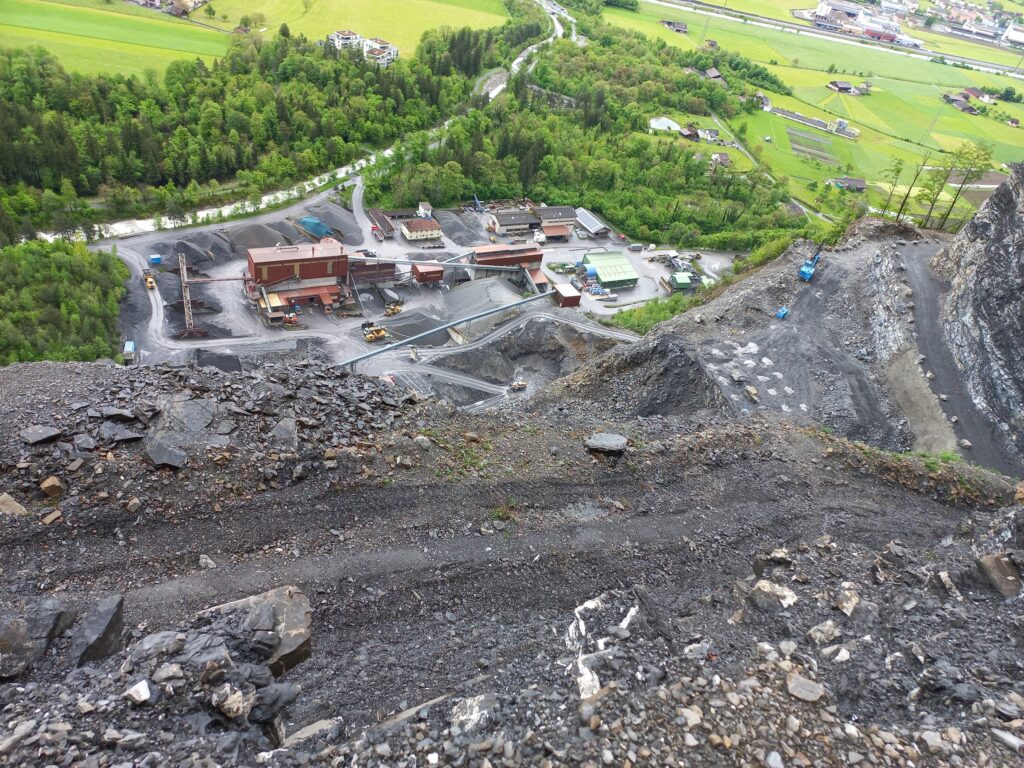
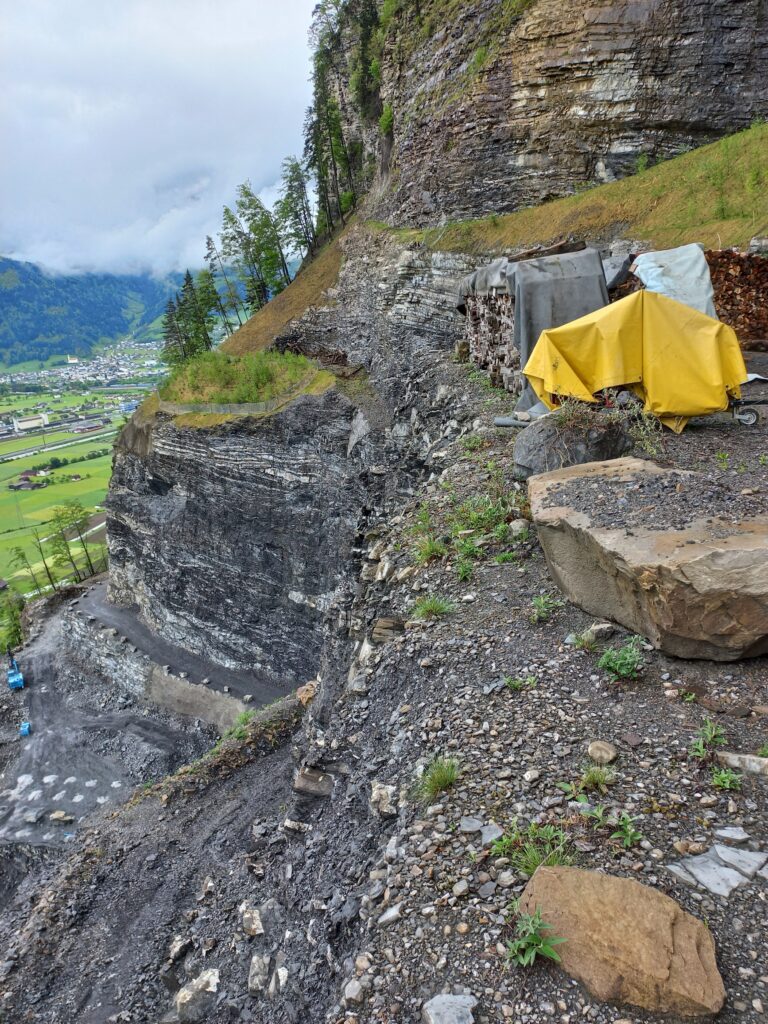
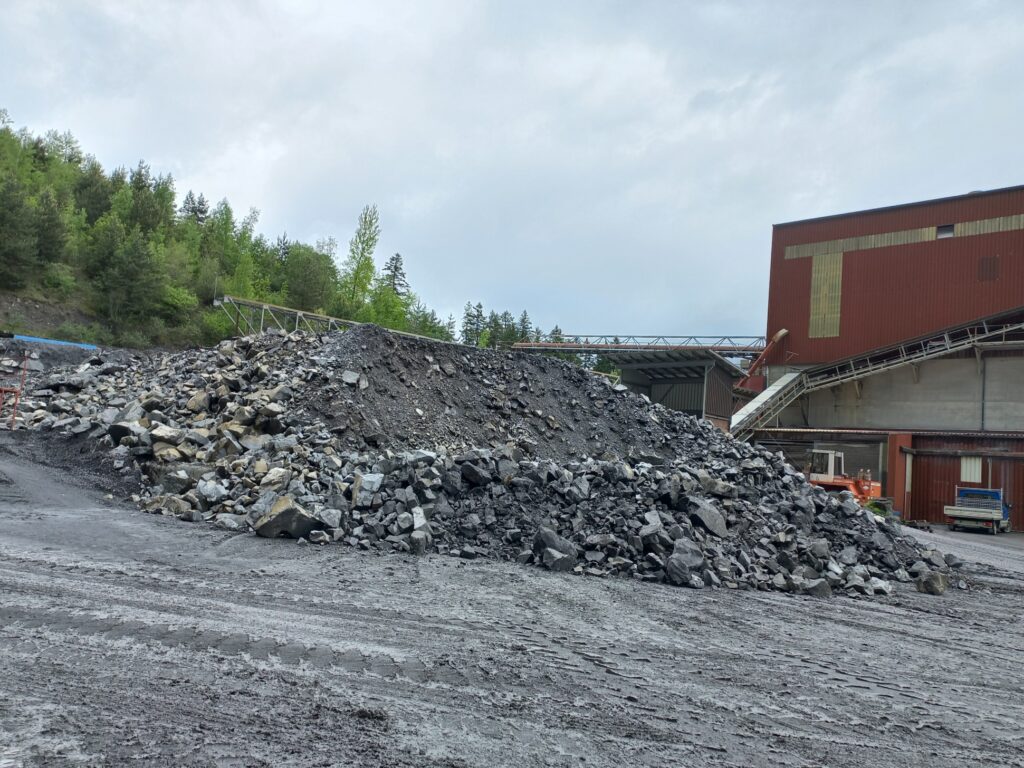
Im zweiten Teil der Führung stellt uns Armando De Col die Fertigungsschritte von den bis zu einer Tonne schweren Felsbrocken zu den Endprodukten her. Armando De Col arbeitet seit über fünfunddreissig Jahren bei der Firma Gasperini und ist mit den Produktionsprozessen und dem Material bestens vertraut. Die grossen Felsbrocken werden in einer ersten Phase mit einem riesigen Steinbrecher (Vorbrecher) in kleinere Brocken zertrümmert. Anschliessend werden diese Brocken je nach der Art des Endproduktes in einer anderen Halle weiter gebrochen und in verschiedene Fraktionen ausgesiebt. Der Bahnschotter wird vor dem Verlad noch gewaschen.
Bei diesen lärmigen und staubigen Verfahren hat der Gesundheitsschutz der Arbeitenden eine sehr hohe Bedeutung – die Anlagen werden wöchentlich vom Staub befreit.
Die eingesetzten Steinbrecher stammen grösstenteils von der Firma Emil Gisler AG im benachbarten Seedorf. Unter dem Markenname Gipo AG konstruiert dieses Unternehmen weltweit eingesetzte Steinbrecher und Aufbereitungsanlagen der Spitzenklasse. Diese Firmengruppe darf die Bezeichnung «Hidden Champion» wohl zu Recht in Anspruch nehmen.
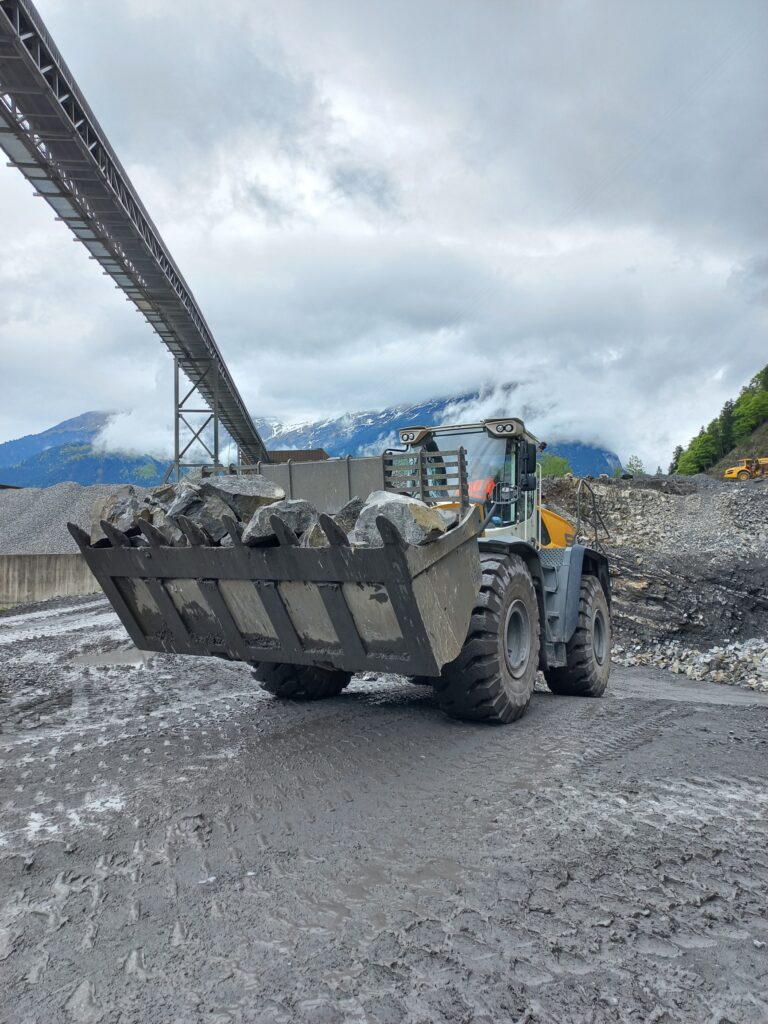
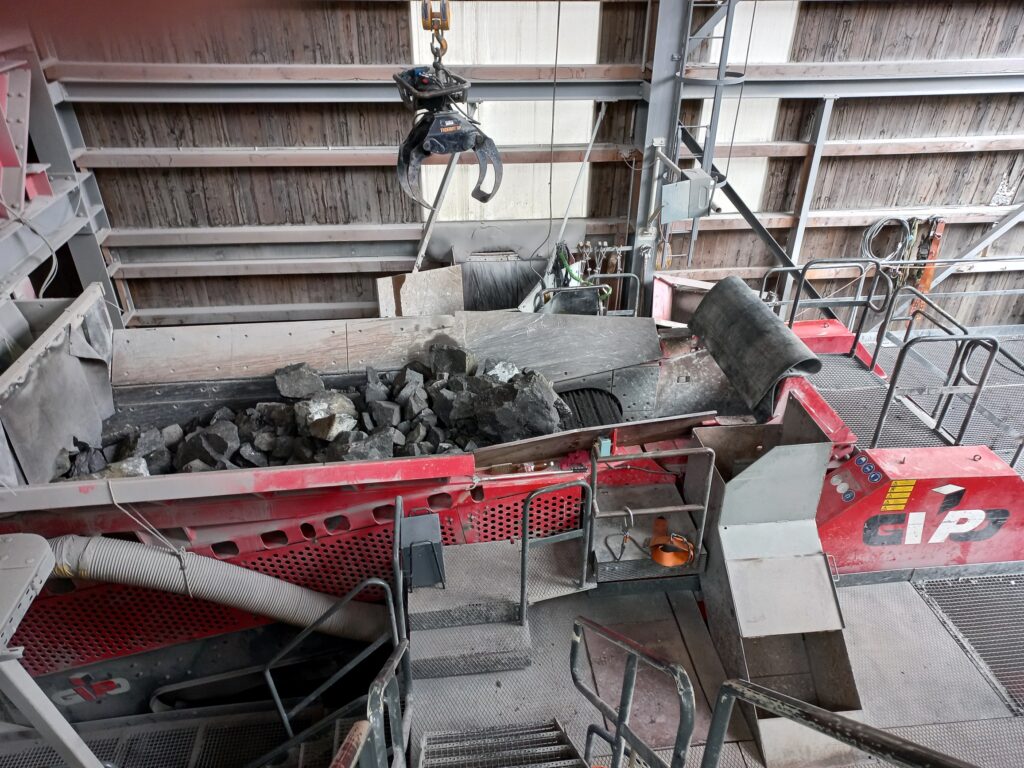
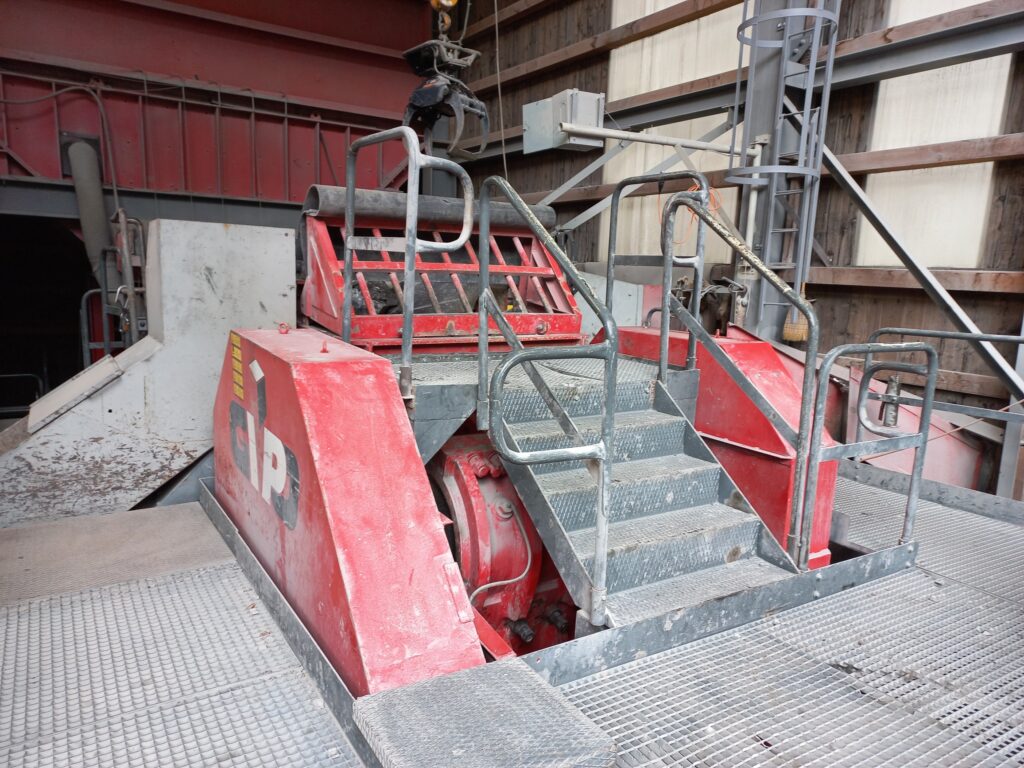
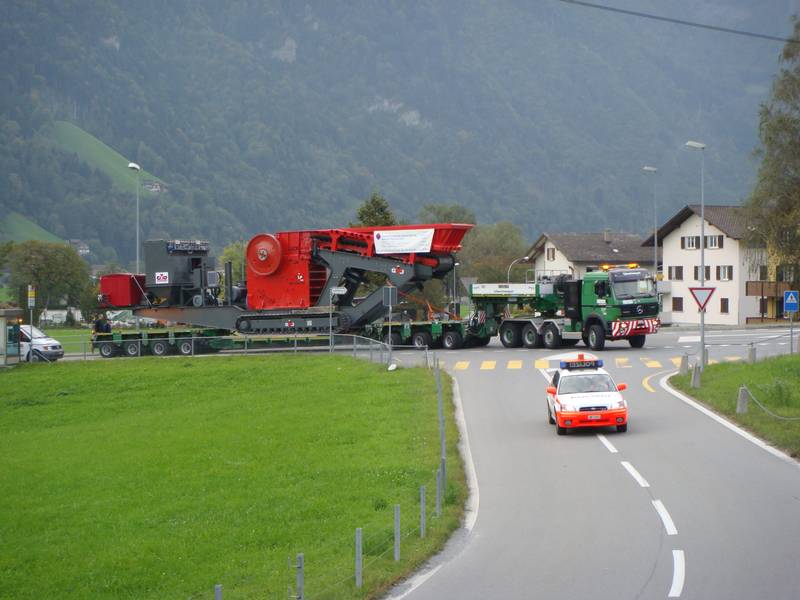
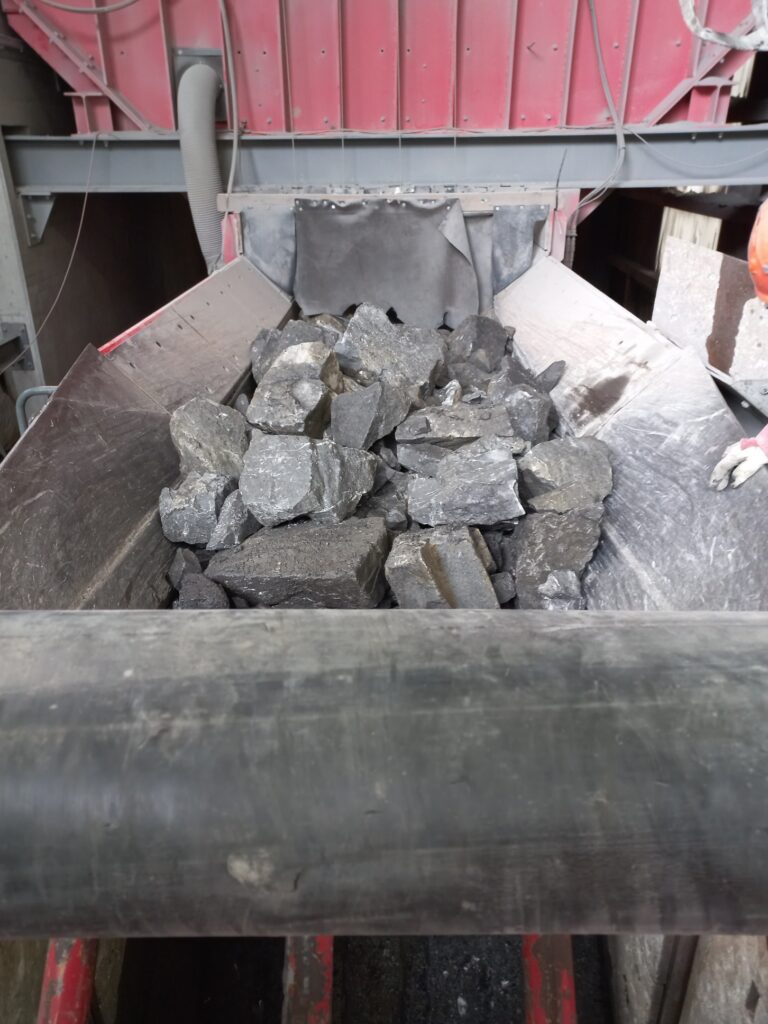
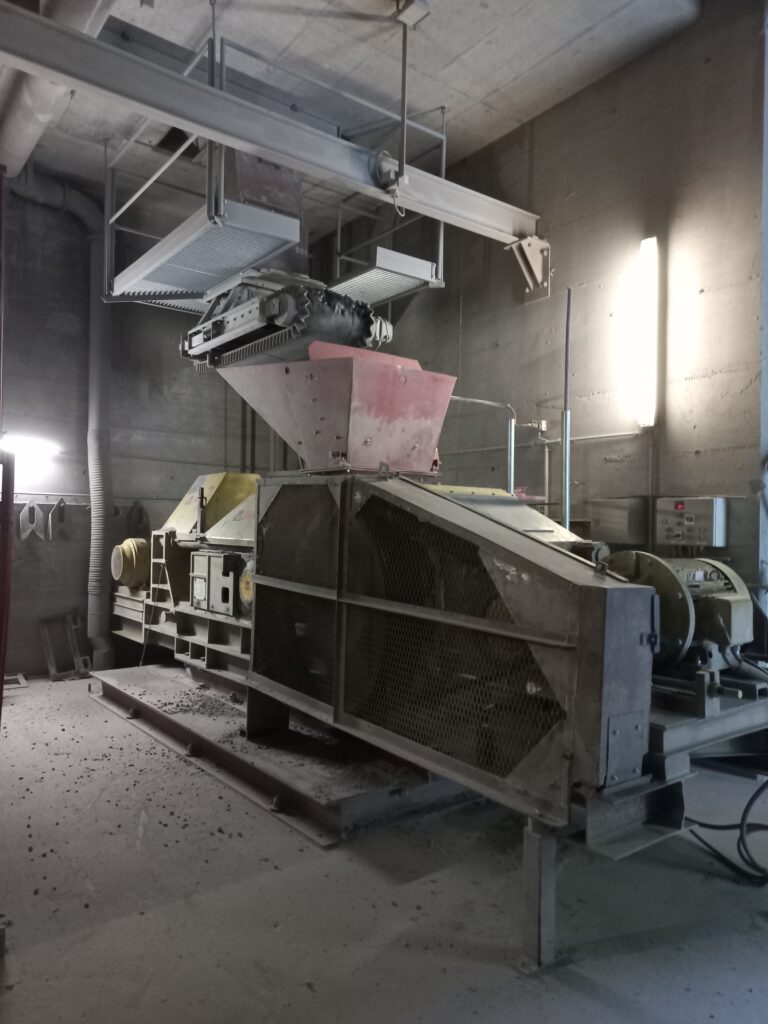
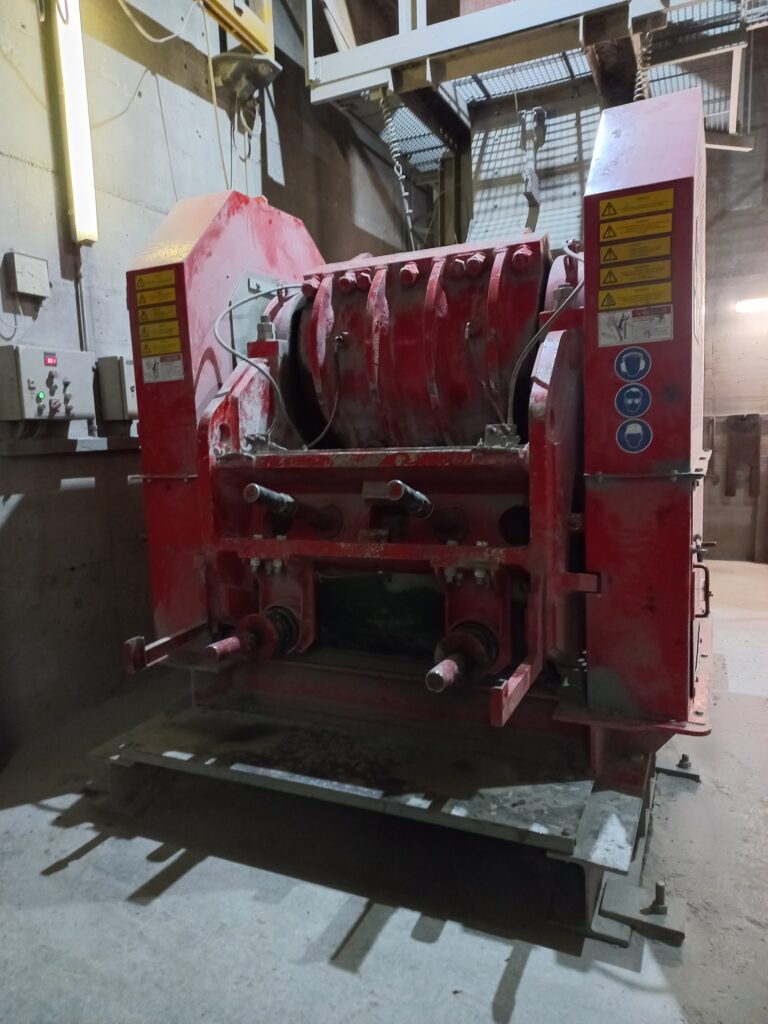

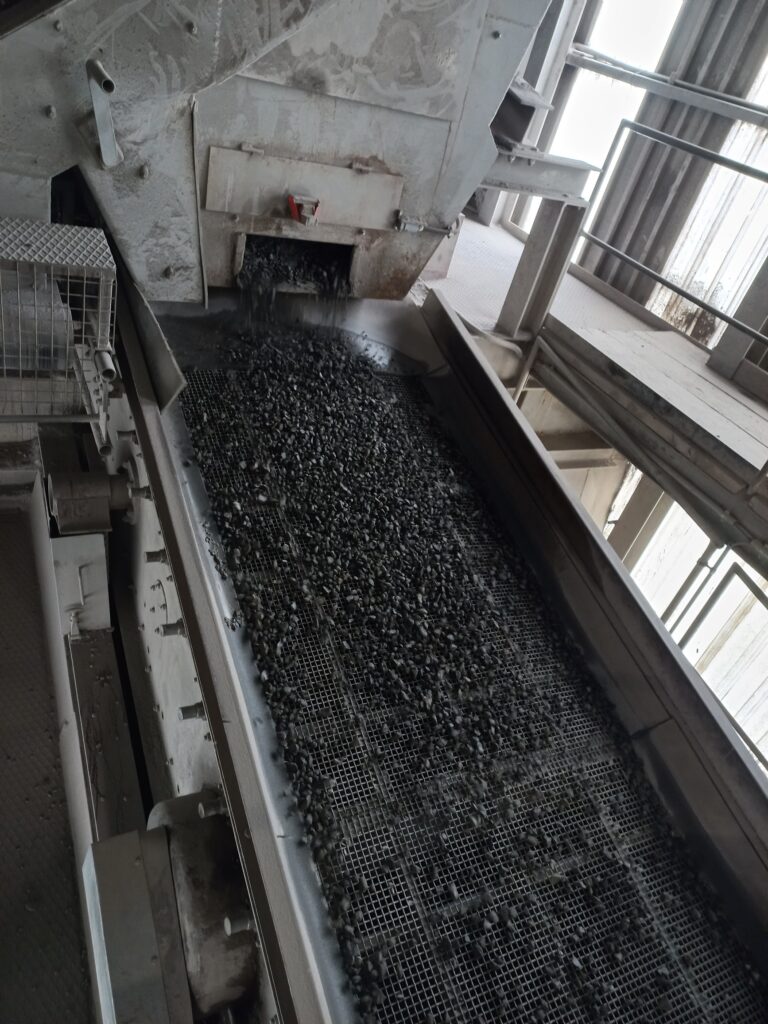
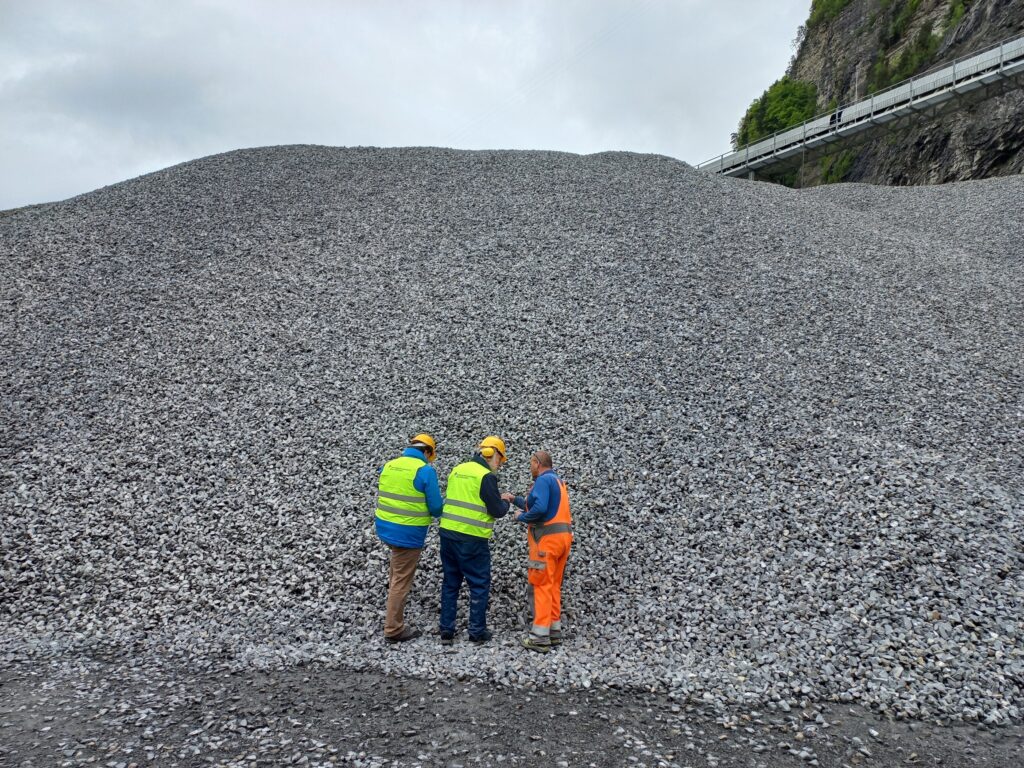
Der feine Imbiss im Anschluss an die eindrückliche Betriebsbesichtigung bot willkommene Gelegenheit zur Vertiefung der erhaltenen Informationen. Kurz vor 13.00 Uhr bedankte sich Lorenz Degen bei Michela Gasperini und Peter Müller für den eindrücklichen Besuch und die grosszügige Gastfreundschaft.
Firma Arnold & Co. AG
Kurz vor 16.00 Uhr begrüsst uns Matthias Steinegger beim Hafen Flüelen zur Besichtigung der Firma Arnold & Co. AG. Matthias Steinegger lässt es sich als Betriebsleiter nicht nehmen, uns sein Unternehmen persönlich vorzustellen. Die Firma Arnold & Co. AG besteht seit etwa 120 Jahren und wird als traditionsbewusstes Familienunternehmen in vierter Generation von Nachkommen der Gründerfamilie geführt. Dank erstklassigen Produkten und einer umsichtigen Geschäftspolitik kann sich Arnold & Co. AG neben Grossunternehmen wie KIBAG oder Holcim AG auf dem Markt behaupten.
Nach einer kurzen Vorstellung des Unternehmens und seiner Geschichte fahren wir mit einem Ledischiff zur Baggeranlage neben dem Reussdelta. Die eindrückliche Anlage wiegt 1’000 Tonnen und verarbeitet den Aushub aus dem an dieser Stelle rund 60 Meter tiefen See zu Sand und Kies in verschiedenen Körnungen. Die maximale Kapazität der eindrücklichen Anlage beträgt 2’500 Tonnen pro Tag. Die Jahresproduktion liegt bei rund 300’000 Tonnen Sand und Kies. Zum Vergleich: Die Reuss lagert gemäss der Ausgabe 2016, Heft 2, der Zeitschrift «Wasser Energie Luft» jährlich durchschnittlich etwa 56’000 m3 Geschiebe im Urnersee ab. Im Katastrophenjahr 1987 waren es sogar weit über eine Million Tonnen.
Nach der Reinigung des Aushubs vom See werden Sand und Kies – dieser in drei Korngrössen – getrennt und auf Ledischiffe verladen und auf dem Seeweg zu den Kunden transportiert. Die Produkte geniessen bei den weiterverarbeitenden Unternehmen dank ihrer Qualität und ihrer Beschaffenheit einen ausgezeichneten Ruf.
Nach der kurzen Einführung werden die Besucher durch das fast 20 Meter hohe Baggerschiff geführt und können vor Ort die verschiedenen Verarbeitungsschritt verfolgen. Die Anlage wird mit Unterwasserleitung mit elektrischem Strom versorgt. Der Strom wird auf dem Festland von einer Spannung von 15’000 Volt auf noch 4’500 Volt transformiert. Die Konzession für den Abbau wird vom Kanton Uri jeweils für 25 Jahre vergeben. Arnold & Co. AG ist seit drei Perioden Inhaberin dieser Konzession.
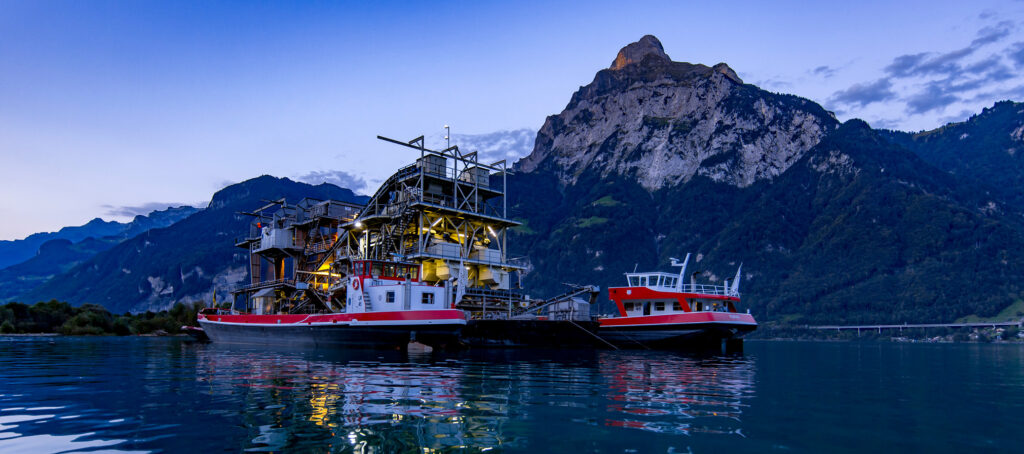
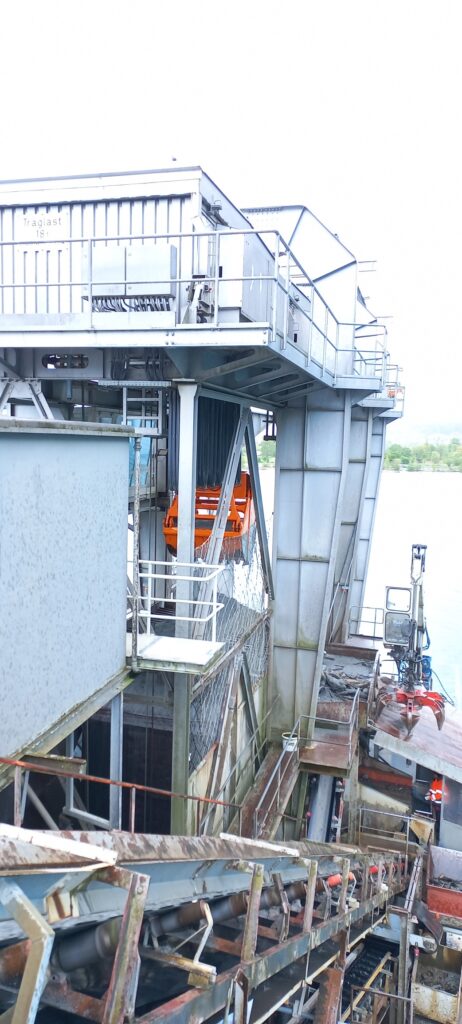
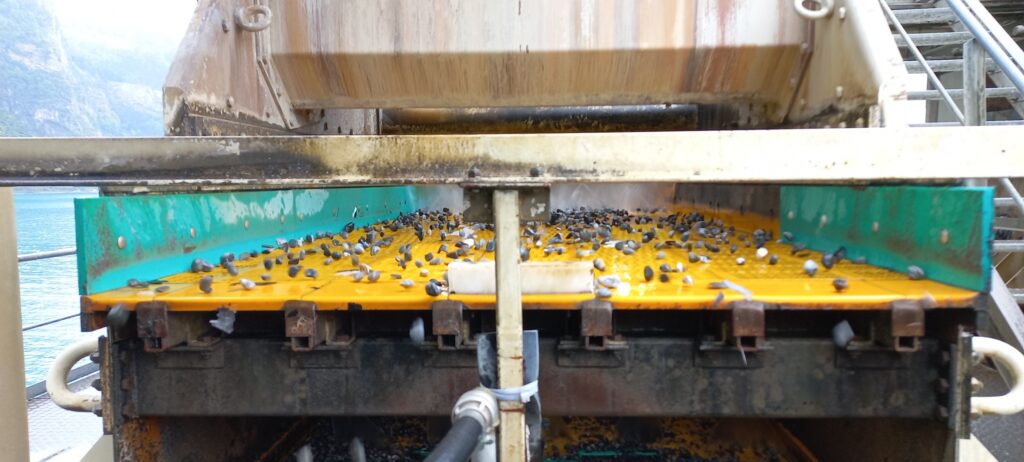
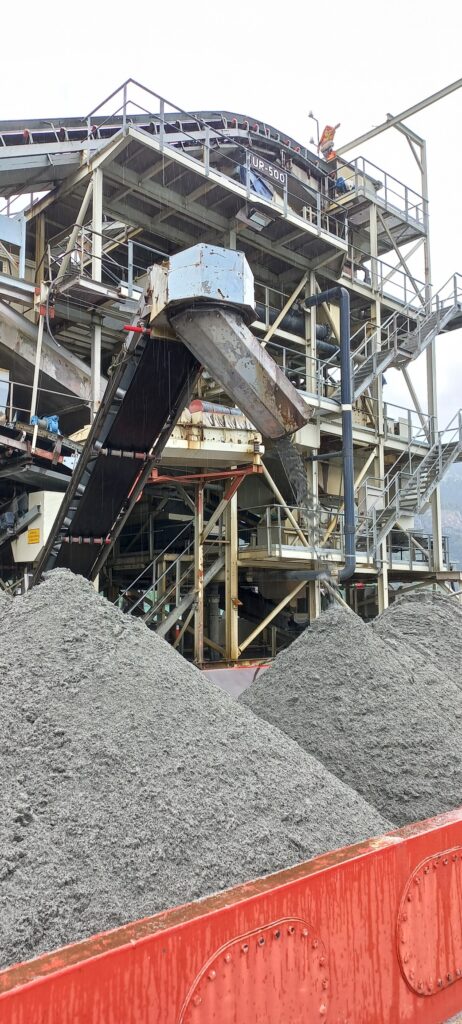
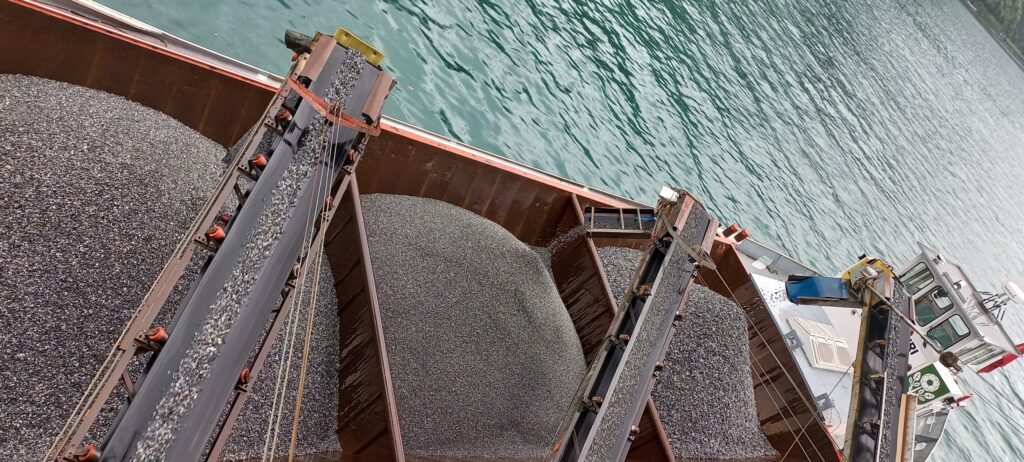
Nach etwa dreissig Minuten gelangen wir mit dem Schiff zurück an den Ausgangspunkt und zum nächsten Höhepunkt unserer Visite. Beim Frachthafen können wir den Entladevorgang eines Zuges mit Ausbruchmaterial aus der zweiten Röhre des Gotthardstrassentunnels verfolgen. Das mit dem Zug aus Göschenen herangeführte Ausbruchmaterial wiegt rund 1’000 Tonnen und wird mit leistungsfähigen Förderanlagen innert einer Stunde über ein Zwischenlager auf das daneben liegende Ledischiff abgeladen. Täglich können bis zu sieben Züge entladen werden – die 7’000 Tonnen Ausbruch entsprechen der maximalen Tagesleistung der Tunnelbohrmaschine.
Wir fahren mit einem voll beladenen Ledischiff zum eigens für den Ablad des Ausbruchs geschaffenen Dock. Unter dem Wasserspiegel sind am Dock grosse Tücher angebracht, die einen kontrollierten Ablad gewährleisten und eine Ausbreitung der feinen Teile im Wasser minimieren. Beeindruckt verfolgen die Besucher, wie sich eine nach der anderen Kammer entleert. Der behutsame Entladevorgang hinterlässt fast den Eindruck, dass sich das Material aus dem Innern des Gotthards gegen das Versenken im See wehren würde.
Mit dem leeren und nun weit aus dem Wasser ragenden Schiff fahren wir zurück ans Ufer. Auf der Rückfahrt zum Hafen weist Matthias Steinegger auf die künstlichen Inseln mit Aushub aus dem Gotthardbasistunnel hin. Diese bieten willkommenen Schutz für Fauna und Flora. Insgesamt wurden 3.5 Mio. Tonnen Ausbruch aus dem Gotthardbasistunnel im See deponiert. Als umweltbewusstes und nachhaltiges Unternehmen besteht zwischen Arnold & Co. AG mit den Umweltorganisationen ein gutes Einvernehmen.

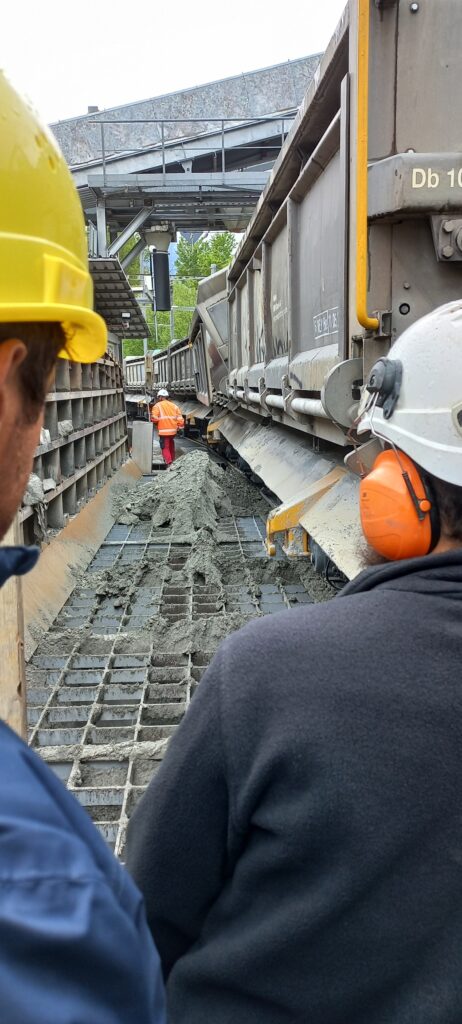
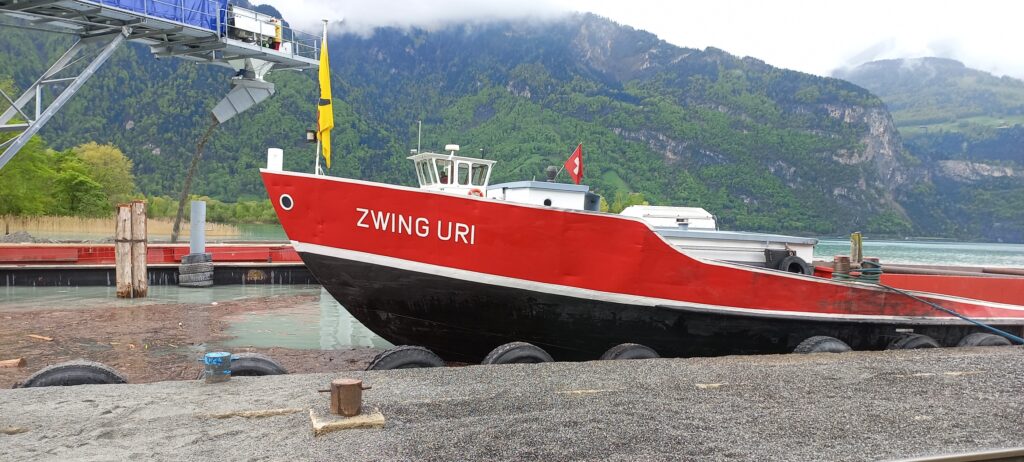
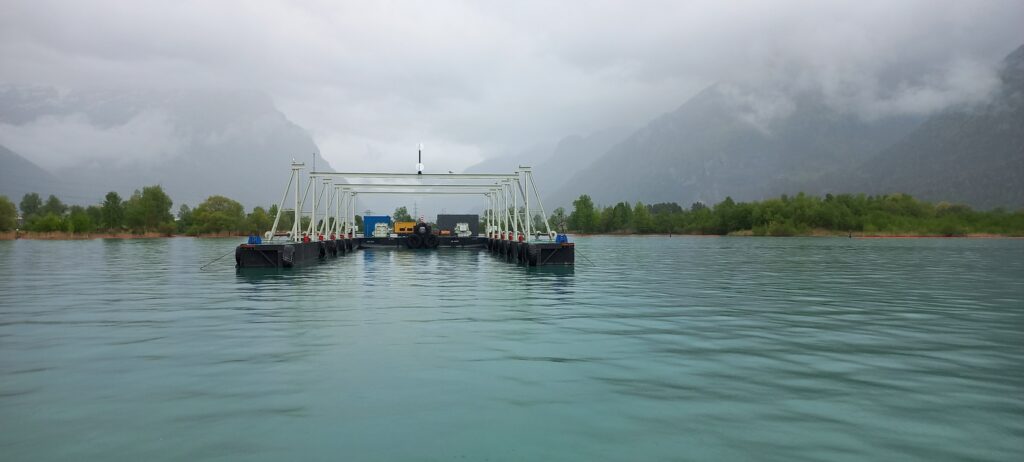
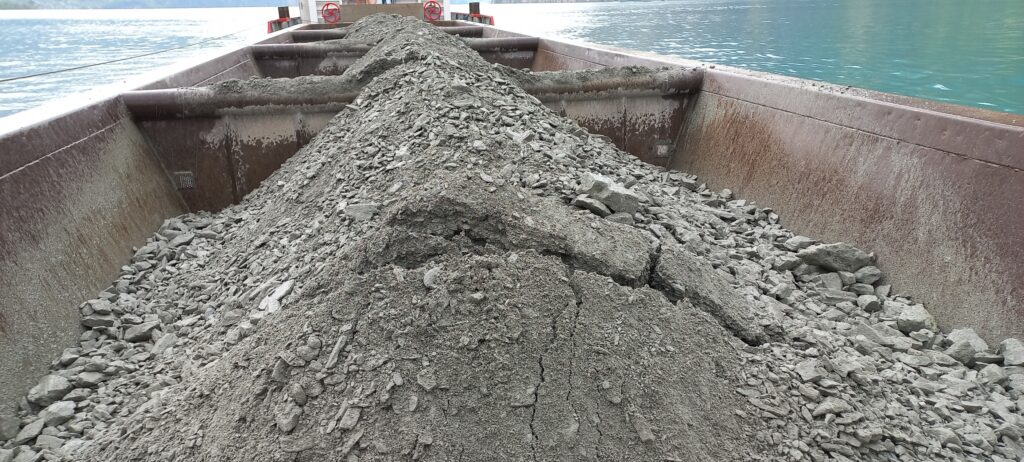
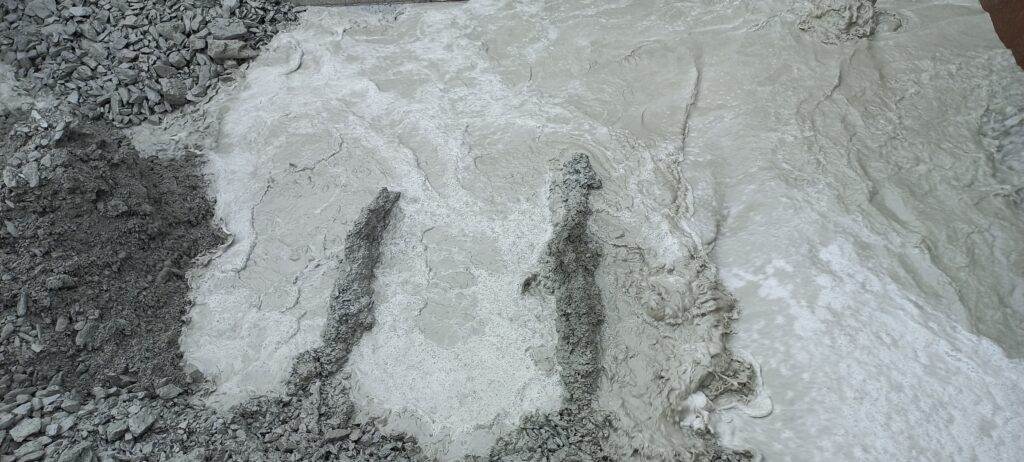

Bei der Ankunft im Hafen lädt uns Matthias Steinegger noch auf dem Schiff zu einem Apéro ein. Dabei erhalten wir weitere interessante Informationen über das Unternehmen. So produziert Arnold & Co. AG jährlich auch zwischen 50’000 und 80’000 m3 Beton und Mörtel. Hergestellt werden gegen 130 verschiedene Beton- und Mörtelarten. Bemerkenswert ist, dass der Zement in Altdorf von den Silowagen der SBB auf LKW verladen wird und für die kurze Distanz auf der Strasse zum Betonwerk gelangt. Flüelen wird seit einigen Jahren von SBB Cargo nicht mehr bedient.
Kurz vor 17.30 Uhr bedankt sich Lorenz Degen bei Matthias Steinegger für die spannende Präsentation der Firma Arnold & Co. AG, worauf sich die beeindruckte Delegation zum Bahnhof Flüelen begibt, um von dort die Rückreise anzutreten.
Abschliessende Bemerkungen
Auch von meiner Seite ein grosses Dankeschön an Lorenz Degen für die eindrückliche Studienreise sowie an die besuchten Firmen für den freundlichen Empfang und die packenden Betriebsbesichtigungen. Beeindruckend, mit welchem Qualitätsbewusstsein und Fachwissen vermeintlich einfache Materialien wie Schotter, Kies und Sand hergestellt werden.
Gegensatz zu früher, wo mit einem Zug bis zu 800 Tonnen Schotter transportiert wurden, ist heute die Maximallast pro Zug wegen dem Mangel einer geeigneten Rangierlokomotive auf 400 Tonnen beschränkt. Infolge dieser Beschränkung erfolgen Lieferungen ins Tessin aber auch in der Deutschschweiz vermehrt mit Lastwagen.
Eine (weitere) Bankrotterklärung der SBB-Güterbahn
Sehr geehrter Herr Hug
Vielen Dank für Ihr Interesse an unserer Website und für Ihren Kommentar.
In der Tat eine besorgniserregende Aussage. Noch viel weniger verständlich ist, dass Flüelen offensichtlich kein Bedienpunkt für SBB Cargo mehr ist und der Zement für das Betonwerk der Firma Arnold & Co. AG von Altdorf mit Lastwagen nach Flüelen transportiert wird. Da fragt man sich schon, ob der Wagenladungsverkehr tatsächlich aufrecht erhalten werden soll. Meine Überzeugung hat gelitten.
Ich wünsche Ihnen weiterhin viel Freude an unserer Website.
Freundliche Grüsse
Ernst Rota